The vacuum brazing furnace is primarily used for quenching, solid solution, aging treatments, and also vacuum brazing and post-brazing heat treatments for various metals. This type of furnace is particularly suitable for brazing stainless steel, high-temperature alloys, and other materials. During the heating process, the parts are placed in a vacuum environment, which prevents oxidation and other issues. As a result, vacuum brazing furnaces are widely used in industries such as aerospace, nuclear energy, electronics, petrochemical, medical equipment, tool manufacturing, and automotive. Below is a detailed description of the vacuum brazing furnace structure:
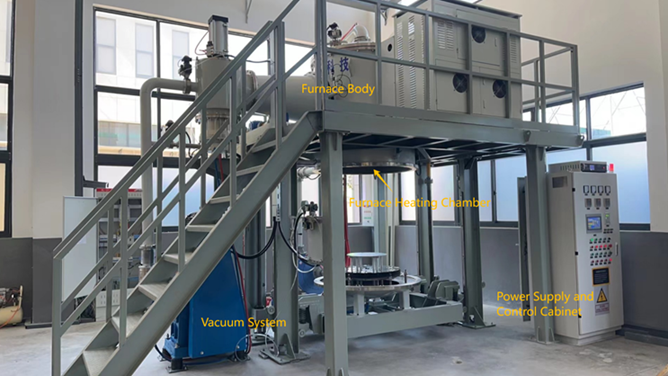
1. Furnace Body
The furnace body includes the furnace shell, furnace door, and other components. Specifically, the furnace shell is a horizontal, double-layer, water-cooled cylinder. The furnace door is hinged to the furnace body, and a rubber seal is placed between the furnace body and the furnace door. Additionally, the furnace body is equipped with a limit switch and an indicator light. These components help monitor and display whether the furnace door is properly closed and locked.
2. Furnace Heating Chamber
The furnace heating chamber is a key part of the vacuum brazing furnace. It consists of heating elements, insulation layers, and the charge platform.
- Heating Elements: Molybdenum strips are used as the heating elements. These strips are evenly arranged around the furnace liner. The molybdenum strips are connected and fixed using molybdenum connectors. This design ensures the furnace heats up quickly and evenly in one controlled temperature zone.
- Insulation Layer: The insulation layer is made from molybdenum sheets, stainless steel sheets, and thermal cotton. The charge platform, which is made from molybdenum beams and columns, is also essential. To prevent the material frame from sticking to the furnace bed, ceramic cushions (95% ceramics) are placed on the beam guides. The charge platform is designed to have sufficient strength to support the load, and it does not deform significantly at high temperatures.
3. Vacuum System
The vacuum system is responsible for generating and measuring the vacuum. It includes multiple vacuum pumps, cold traps, pneumatic valves, and connecting pipes. This system ensures that the furnace reaches the required working vacuum and ultimate vacuum levels. For this furnace, a three-stage vacuum pump has been selected, which allows it to meet various vacuum requirements.
4. Gas Charging System
The gas charging system consists of a gas storage tank, automatic and manual charging valves, a pressure gauge, pressure sensors, and safety valves. The gas cooling system operates on an internal circulation method. Notably, the charging pressure is adjustable from 1 bar to 12 bar (gauge pressure), depending on process requirements. The system can be set to operate automatically when gas needs to be charged. Additionally, manual valves are included for emergency situations.
5. Air Cooling System
The air cooling system includes a motor with a frequency converter, a high-capacity fan, a copper heat exchanger, a pneumatic butterfly valve, and connecting pipes. When air cooling is selected, cooling gases, such as ammonia or argon, enter the furnace through the charging valve. As soon as the furnace pressure reaches a level close to the room pressure, the fan activates, and the cooling gas circulates within the furnace to absorb heat. The charging valve opens and closes according to preset pressure levels. Cooling nozzles inside the furnace further enhance rapid cooling.
6. Water Cooling System
The water cooling system primarily cools components such as the furnace door, furnace shell, heat exchangers, and vacuum units. It is equipped with a water distribution pipe and a return water pipe, each controlled by independent valves. Water flow sensors are installed on each branch, allowing real-time monitoring. Furthermore, the system includes pressure and temperature gauges that trigger alarms and interlocking protection when the water pressure is low or the return water temperature is too high. The system also has dual water inlet connections, which can be linked to an emergency water supply system. This ensures that the equipment continues to receive cooling water during power outages, preventing potential damage.
In summary, the vacuum brazing furnace is a versatile piece of equipment used for metal treatments such as quenching, solid solution, aging, and brazing. It is particularly effective for materials like stainless steel and high-temperature alloys due to its ability to prevent oxidation during the heating process by maintaining a vacuum environment. The vacuum brazing furnace structure such as the furnace body, heating elements, insulation layers, vacuum system, gas charging system, and cooling systems, all of which work together to ensure efficient, uniform heating and temperature control. These furnaces find applications in various industries, including aerospace, electronics, petrochemical, medical, and automotive.