There are four main methods for brazing aluminum alloys: dry air chloride flux brazing, salt bath brazing, nitrogen-protected flux-free brazing, and vacuum flux-free brazing. The dry air and salt bath methods use chloride flux, which leaves corrosive residues after brazing. These residues require removal, and cleaning consumes large amounts of fresh water, leading to environmental pollution. As a result, research into flux-free brazing techniques has intensified, giving rise to vacuum aluminum brazing.
1. Mechanism and Features of Vacuum Aluminum Brazing
During aluminum alloy brazing, the oxide film on the surface prevents proper wetting and flow of the filler metal. If the oxide film isn’t removed, high-quality joints cannot form. To remove the oxide film and prevent re-formation during brazing, a small amount of magnesium is added to the filler metal. Magnesium breaks up the oxide film, allowing the filler metal to spread and wet the surface more effectively.
Vacuum aluminum brazing involves both physical and chemical changes. The coefficient of linear expansion of aluminum oxide is about one-third that of aluminum. As the temperature exceeds 400°C, thermal stress can cause the oxide film to crack and expose the pure aluminum surface. Magnesium in the filler metal evaporates at temperatures above 550°C, creating a magnesium-rich atmosphere that prevents oxidation. This atmosphere also helps infiltrate the oxide film and further break it down, allowing the filler metal to wet the fresh surface and form the brazed joint.
This process must occur in a high vacuum, typically around 10-3 Pa. If the vacuum is too low, magnesium evaporates and combines with oxygen and moisture, which prevents the formation of a protective magnesium atmosphere. As a result, the aluminum surface re-oxidizes, and the filler metal cannot wet the surface.
For heat exchanger products, the workpieces have large surface areas and adsorb a significant amount of gas. During heating, outgassing reduces the vacuum level. To maintain a high vacuum, a vacuum system with a high pumping speed is necessary.
The melting point of Al-Si-Mg filler metal is close to that of aluminum, so the brazing temperature range is narrow, typically between 595°C and 615°C. Heat exchanger structures are usually large with uneven temperature distribution, and they are made of thin-walled materials. Therefore, strict temperature control is needed, usually within ±5°C, which requires zoned temperature control.
2. Applications of Vacuum Aluminum Brazing
Vacuum aluminum brazing is widely used across industries such as aerospace, petrochemicals, electronics, air separation, automotive, shipbuilding, and refrigeration. Heat exchangers are one of the key applications. Specific products include automotive air conditioning evaporators and condensers, radiators, oil coolers, intercoolers, and plate-fin heat exchangers for air separation equipment.
Typical Brazing Examples
Automotive Radiators (Water Tanks)
The radiator core is brazed in a vacuum furnace using flat tubes, heat fins, and end plates. The flat tubes are made by seam-welding composite plates with filler metal on one side. The base material is LF21, and the filler metal is Al-Si-Mg alloy. The heat fins are not coated with filler metal but are folded into a wavy shape using a roll machine with holes for heat dissipation. Radiators can have one or multiple rows of tubes, with a trend toward single-row designs.
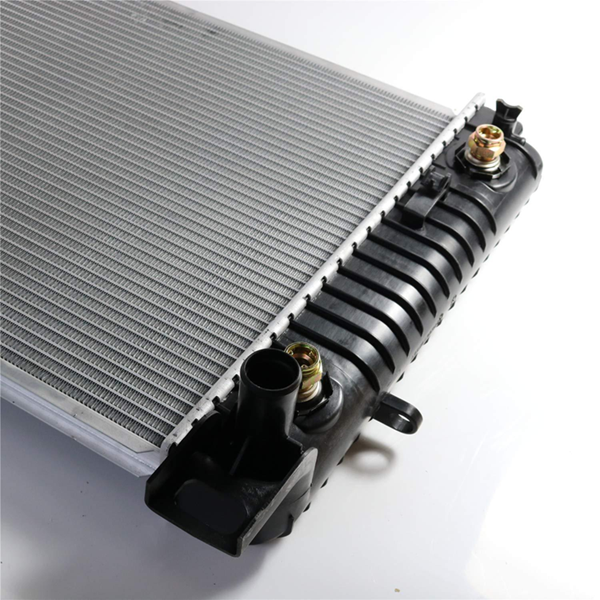
Intercoolers
Intercoolers in heavy-duty trucks have a structure similar to radiators, but the tubes are made from extruded porous flat tubes, which do not contain filler metal. The heat fins are composite plates with filler metal. The seams between the flat tubes, end plates, and heat fins can be brazed in a vacuum furnace in one step.
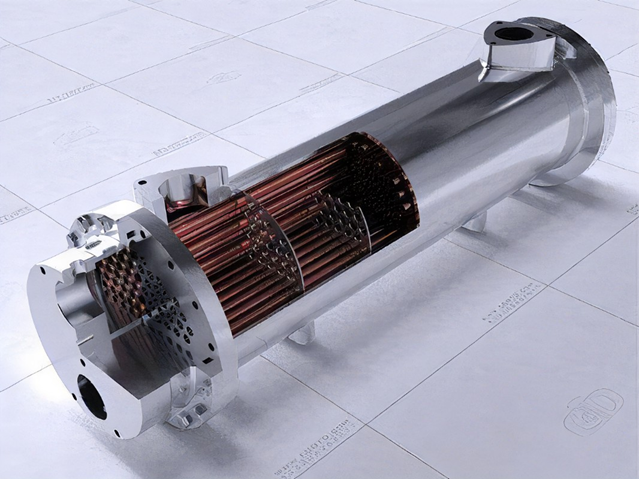
Evaporators are generally made with serpentine tubes. The tubes are extruded from pure aluminum or LF21 aluminum alloy and bent into a serpentine shape. The heat fins are made from composite thin plates and inserted into the tubes, then brazed in the furnace. Condenser tubes and fins are narrower, but the overall structure is larger. Since condensers must withstand higher internal pressure, the flat tubes used in condensers are usually thicker than those in evaporators.
4. Advantages of Vacuum Aluminum Brazing
Vacuum aluminum brazing is an advanced process that uses no flux in a vacuum atmosphere. Compared to traditional flux brazing methods, it offers several benefits:
No flux or salts are used, avoiding harmful gas emissions during heating, eliminating the need for cleaning, and preventing environmental pollution.
The high vacuum process ensures thorough degassing, preventing defects like porosity and slag inclusions, and producing dense seams and joints.
No residual flux or salts left on the workpieces means no corrosion, which extends product lifespan.
The brazed surfaces are clean, bright, and aesthetically pleasing.
5. Molybdenum Strip Vacuum Brazing Furnace
A molybdenum strip vacuum brazing furnace is a specially designed equipment used for brazing in high-temperature vacuum environments, utilizing molybdenum as the main heating element or structural material. This equipment is widely used for welding high-melting-point materials, high-temperature alloys, and dissimilar materials due to its excellent high-temperature performance and vacuum compatibility.
For more details on the vacuum brazing furnace, please click on the image link for the molybdenum strip vacuum brazing furnace.
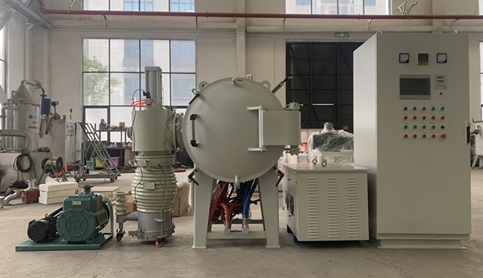