Although there are many different types of batch vacuum induction furnaces in terms of quantity, from an industrial production perspective, the continuous-type furnace will be the main equipment. Batch furnaces are typically used for experimental research, small-batch production, or trial runs, where frequent batch changes are necessary. However, as industrial production demands greater stability, efficiency, large-scale output, and consistent product quality, continuous-type vacuum induction furnaces are gradually becoming the mainstream choice, especially in industries like high-temperature alloys and large alloy casting.
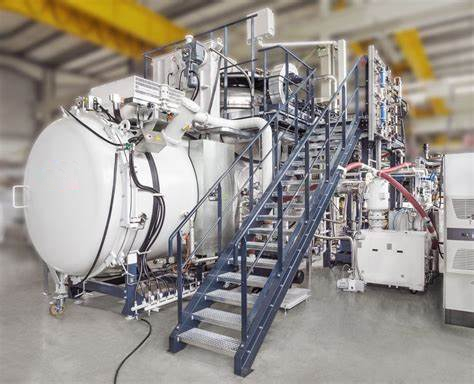
Application Trends in High-Temperature Alloy Industry
For example, in the high-temperature alloy industry, the application of vacuum induction furnaces is particularly evident. China has a significant market presence in high-temperature alloy production, especially in the field of deformed high-temperature alloys. Large steel mills, such as Fushun Steel (Fugang) and Shanghai Steel (Shangang), primarily use large continuous vacuum induction furnaces. These furnaces typically have capacities ranging from 8 to 20 tons, with some companies even planning to introduce 30-ton class large continuous vacuum induction furnaces.
These furnaces not only meet the growing demand for large-scale production but also ensure the stability and efficiency of the process, thereby guaranteeing the high purity and consistency of alloys.
Deformed high-temperature alloys, such as nickel-based and cobalt-based alloys, are widely used in aerospace, energy, and chemical industries. The production process requires high precision, stability, and efficiency. Continuous vacuum induction furnaces are able to maintain a steady melting process without the need for frequent furnace changes. This increases production efficiency and ensures precise control over alloy composition and temperature. As a result, the consistency of the alloy quality is maintained during batch production, meeting the industry’s high-quality requirements.
Continuous-Type Vacuum Induction Furnace in Casting High-Temperature Alloys
In addition to deformed high-temperature alloys, continuous vacuum induction furnaces also play a critical role in the production of casting high-temperature alloys. Leading casting companies in China, such as Aerospace Materials Institute (AMS) and Metal Research Institute, mainly rely on 0.5 to 3-ton continuous vacuum induction furnaces. These companies specialize in the casting of aerospace alloys, metals for energy applications, and other high-performance alloys. The continuous melting process is essential in these industries, where precise control of alloy composition, prevention of contamination, and avoidance of oxidation are critical.
Unlike batch furnaces, continuous vacuum induction furnaces allow for uninterrupted production, which is crucial for casting high-temperature alloys. These alloys often involve complex compositions and high-melting-point metals (such as cobalt-based and nickel-based alloys), which require strict control over temperature, time, and environmental conditions. Continuous furnaces provide a stable environment for heating and melting, ensuring the precise control of temperature, atmosphere, and alloy composition. This results in consistent quality and reduced human error.
Industrial Advantages of Continuous-Type Vacuum Induction Furnaces
From the perspective of industrialized production, continuous-type vacuum induction furnaces offer several significant advantages, making them the main equipment for large-scale and high-precision production. These advantages include:
- Improved Production Efficiency: Continuous furnaces eliminate the need for frequent furnace changes and downtimes, allowing for uninterrupted production. This increases overall production efficiency and meets the demands of large-scale, long-duration manufacturing.
- Reduced Energy Consumption: The continuous production model ensures that heating and melting processes are more uniform. This reduces energy waste and unnecessary consumption, helping companies lower production costs.
- Enhanced Alloy Quality: Continuous vacuum induction furnaces provide a more stable production environment, minimizing fluctuations. This helps ensure consistent alloy composition and stability, improving the quality of the final product.
- Automation and Intelligent Control: Modern continuous vacuum induction furnaces are often equipped with automated and intelligent control systems. These systems manage temperature, atmosphere, and alloy composition, significantly improving precision and reducing the risks of human error.
- Adaptability to Diverse Demands: With flexible control systems, continuous furnaces can be adjusted for different materials, alloy compositions, and production needs. This allows them to meet the growing and diverse demands of high-temperature alloys and specialty metals in the market.
Future Development Trends
As industrial production continues to grow globally, especially in industries such as aerospace, automotive, electronics, and metallurgy, the demand for high-performance, high-precision materials will increase. Continuous vacuum induction furnaces will play an increasingly important role in global manufacturing. China’s manufacturing sector continues to advance in the production of high-temperature alloys and other precision materials. In the future, companies will adopt larger, automated, and more intelligent continuous vacuum induction furnaces to enhance production capacity, reduce costs, and improve product quality.
Moreover, as manufacturing industries pay more attention to environmental protection and sustainability, the energy efficiency and environmental performance of continuous vacuum induction furnaces will become key competitive factors. Lower energy consumption, reduced emissions, and higher material recovery rates will be essential to the future development of continuous vacuum induction furnaces.
Conclusion
In summary, continuous-type vacuum induction furnaces are set to gradually replace batch furnaces and become the primary equipment for the production of high-temperature alloys, large alloy castings, and other high-performance materials. With advancements in technology and changes in industrial demands, continuous furnaces will play an increasingly vital role in the metallurgy industry. They will help drive the formation of new industrial production models that are more efficient, precise, energy-saving, and sustainable.