The Vacuum Induction Melting Furnace (VIM) is primarily used for melting precision alloys, electromagnetic materials, alloy steels, and high-temperature alloys. In a vacuum environment, it becomes easier to reduce or eliminate harmful elements such as nitrogen, hydrogen, oxygen, and carbon from metals. Furthermore, this allows for adjustments to the chemical composition of alloying elements. As a result, it significantly improves material properties, including toughness, fatigue strength, corrosion resistance, high-temperature creep resistance, and magnetic permeability in magnetic alloys. Below is a detailed introduction to the design of the vacuum system for a vacuum induction melting furnace.
Furnace Classification
Vacuum induction furnaces are generally classified in two ways: based on furnace structure and product type. In terms of structure, they are divided into batch-type and semi-continuous furnaces. Additionally, according to the products they produce, they can be categorized into deformation alloy melting furnaces and high-temperature master alloy melting furnaces.
Large Vacuum Induction Melting Furnace Vacuum System Design
Large vacuum induction melting furnaces typically require customized designs. These furnaces are tailored to specific melting processes, and their structure varies depending on requirements. The furnace consists of multiple systems, such as the vacuum generation system, power and melting system, cooling water system, hydraulic system, pneumatic system, electrical control system, feeding system (top and side feeding), temperature measurement system (immersion-type and infrared), sampling system, window and camera system, tilting furnace casting device, and trough casting system.
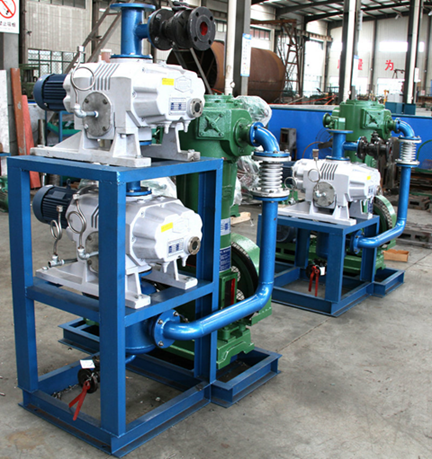
Vacuum System Design
The vacuum system is a critical component of vacuum melting equipment. For large, multifunctional vacuum induction melting furnaces, the vacuum system design is complex and large-scale. It is customized based on the technological process. The vacuum system includes several units, such as the vacuum unit, vacuum piping, vacuum valves, flow transmitters, vacuum filtration system, vacuum pressure sensors, temperature sensors, safety devices, dust removal systems, and flexible connectors.
Vacuum Unit Configuration
The vacuum unit is designed according to the user’s process specifications. The VIM vacuum system consists of three types of pumps: a mechanical pump, a Roots pump, and an oil diffusion (boosting) pump.
The main parameters for the vacuum system include the ultimate vacuum and the rise rate or leak rate.
- Ultimate Vacuum: This parameter measures the quality of the welding and fabrication of the vacuum chamber. The standard range is typically between 0.07 Pa and 0.1 Pa. This vacuum level is assessed based on the vacuum gauge reading, and it does not depend on evacuation time.
- Rise Rate or Leak Rate: The units for this parameter are Pa/h and Pa.L/s. It is used to evaluate the reliability of various seal connections (dynamic and static seals). Generally, this value ranges from 1-3 Pa/h or 30-50 Pa.L/s.
Vacuum System Testing and Design Conditions
Typically, the rise rate is used to evaluate the performance of the vacuum chamber. This is usually performed through evacuation and pressure-holding tests. For example, in the case of a 6-ton large vacuum induction melting furnace, the vacuum design conditions are as follows:
- Melting Chamber: The evacuation rate should reach 0.1 Pa within 30 minutes, with a working vacuum of 1 Pa.
- Mold Chamber: The evacuation rate should reach 5 Pa within 20 minutes.
- Feeding Chamber: The evacuation rate should reach 5 Pa within 5 minutes.
Vacuum Generation Unit Configuration
Based on the vacuum design conditions, the vacuum generation unit configuration for the melting furnace is as follows:
- High Vacuum Configuration:
- 3 EDWARDS series 30B5M oil booster pumps, each with an evacuation rate of 12,500 L/s.
- 1 ZIP-2500 Roots pump and 1 ZIP-600 Roots pump.
- 2 front-end 2-H150D mechanical pumps.
- Low Vacuum Configuration:
- 3 ZIP-2500 Roots pumps and 3 ZIP-600 Roots pumps.
- 6 front-end 2-H150D mechanical pumps.
Conclusion
The design of the vacuum system for a vacuum induction melting furnace is customized according to specific process requirements. The key focus is ensuring that all components have proper sealing, the evacuation rate meets the set standards, and the vacuum levels are achieved as required. Through the use of both high and low vacuum pump configurations, the system is able to meet the vacuum needs during the melting, molding, and feeding processes. Consequently, this ensures the smooth and efficient operation of the melting process.